收藏词条 编辑词条 粉末冶金工艺
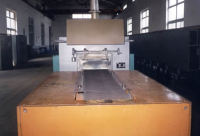
(一)粉末制备
制取粉末:主要取决于该材料的性能及制取方法的成本。粉末的形成是将能量传递到材料,从而制造新生表面的过程。例如,一块1m3的金属可制成大约2×1018个直径为1μm的球形颗粒,其表面积大约为6×106 m2。要形成这么大的表面,需要很大的能量。
制取方法:机械法和物理化学法两大类。机械法制取粉末是将原材料机械地粉碎,而化学成分基本不发生变化的工艺过程;物理化学法则是借助化学或物理的作用,改变原材料的化学成分或聚集状态,而获得粉末的工艺过程。
但是,在粉末冶金生产实践中,机械法和物理化学法之间并没有明显的界限,而是相互补充的。例如,可使用机械法去研磨还原法所得粉末,以消除应力、脱碳以及减少氧化物。
1.机械粉碎法 机械粉碎是靠压碎、击碎和磨削等作用,将块状金属、合金或化合物机械地粉碎成粉末。依据物料粉碎的最终程度,可以分为粗碎和细碎两类。以压碎为主要作用的有碾碎、辊轧以及鄂式破碎等;以击碎为主的有锤磨;属于击碎和磨削等多方面作用的机械粉碎有球磨、棒磨等。实践表明,机械研磨比较适用于脆性材料,塑性金属或合金制取粉末多采用涡旋研磨、冷气流粉碎等方法。
(1)机械研磨法 包括减小粉末粒度;合金化;固态混料;改善、转变或改变材料的性能等。研磨后的金属粉末会有加工硬化、形状不规则、出现流动性变坏和团块等特征。
(2)机械合金化 是一种高能球磨法。用这种方法可制造具有可控细显微组织的复合金属粉末。它是在高速搅拌球磨的条件下,利用金属粉末混合物的重复冷焊和断裂,进行机械合金化的。也可以在金属粉末中加入非金属粉末来实现机械合金化。用机械合金化制造的材料,其内部的均一性与原材料粉末的粒度无关。因此,用较粗的原材料粉末(50~100μm)可制成超细弥散体(颗粒间距小于1μm)。制造机械合金化弥散强化高温合金的原材料,是工业上广泛采用的纯金属粉末,粒度约为1~200μm。
(3)涡旋研磨 在涡旋研磨中一方面依靠冲击作用,另一方面还依靠颗粒间、颗粒与工作室内壁间以及颗粒与回转打击子相碰时的磨损作用。这种方法最初是用来生产磁性材料使用的纯铁粉,以及各种合金钢粉末的。由于涡旋研磨所得粉末较细,为了防止粉末被氧化,在工作室中可以通入惰性气体或还原性气体作为保护气氛。
(4)冷气流粉碎 利用高速高压的气流作为载体,带着较粗的颗粒,通过喷嘴轰击位于击碎室中的靶子后,气流压力立即从7MPa的高压降到0.1MPa,发生绝热膨胀,从而使金属靶和击碎室的温度降到室温以下,甚至零度以下,并将冷却了的颗粒粉碎。气流压力愈大,制得的粉末粒度愈细。冷气流冲击方法适用于粉碎硬质的、以及比较昂贵的材料,可迅速将6目或更小的颗粒原料变成微米级的颗粒。该方法工艺简单、生产费用低、作业温度低(可防止氧化和自燃)、能保持高纯度以及控制被粉碎材料的粒度。
2.雾化法 各种雾化高质量粉末与新的致密技术相结合,出现了许多粉末冶金新产品,其性能往往优于相应的铸锻产品。
雾化法是将液体金属或合金直接破碎,形成直径小于150μm的细小液滴,冷凝而成为粉末。该法可以用来制取多种金属粉末和各种合金粉末。实际上,任何能形成液体的材料都可以通过雾化来制取粉末。
制造大颗粒粉末时,只要让熔融金属通过小孔或筛网自动注入空气或水中,冷凝后便得到金属粉末。这种方法制得的粉末粒度较粗,一般为0.5~1mm,它适于制取低熔点金属粉末。
借助高压水流或高压气流的冲击来破碎液流,称为水雾化或气雾化,也称二流雾化,如图1所示;用离心力破碎液流称为离心雾化,如图2所示;在真空中雾化叫做真空雾化,如图3所示;利用超声波能量来实现液流的破碎称作超声波雾化,如图4所示。
图1 水雾化和气雾化示意图
a)水雾化 b)气雾化
图2 离心雾化示意图
图3 真空(溶气)雾化示意图
图4 超声雾化示意图
3.还原法 用还原剂还原金属氧化物及盐类来制取金属粉末是一种广泛采用的制粉方法。还原剂可呈固态、液态或气态,被还原的物料也可以是固态、气态或液态物质。用不同还原剂和被还原的物质进行还原作用来制取粉末的例子见表1。
表1 还原法广义的使用范围
被还原物料 |
还原剂 |
举 例 |
备 注 |
固体 固体 固体 |
固体 气体 熔体 |
FeO+C→Fe+CO WO3+3H2→W+3H2O ThO2+2Ca→Th+2CaO |
固体碳还原 气体还原 金属热还原 |
气体 气体 气体 |
固体 气体 熔体 |
—— WCl6+3H2→W+6HCl TiCl4+2Mg→Ti+2MgCl2 |
—— 气相氢还原 气相金属热还原 |
溶液 溶液 熔盐 |
固体 气体 熔体 |
CuSO4+Fe→Cu+FeSO4 Me(NH3)nSO4+H2→Me+(NH4)2SO4+(n-2)NH3 ZrCl4+KCl+Mg→Zr+产物 |
置换 溶液氢还原 金属热还原 |
还原是通过还原剂夺取氧化物或盐类中的氧(或酸根),而使其转变为金属元素和低价氧化物(低价盐)的过程。最简单的反应可用下式表示:
MeO+X→Me+XO
式中 Me——生成氧化物MeO的任何金属;
X——还原剂。
对于还原反应来说,还原剂X对氧的化学亲和力必须大于被还原金属对氧的亲和力。
此外,还可以通过气相沉积法和液相沉淀法来制取金属粉末。
综上所述,制取粉末的方法是多种多样的,并且在工程中应用的所有金属材料几乎都可以加工成为粉末形态。在选择制取粉末的方法时,应该考虑到对粉末所提出的性能要求和遵循的经济原则。当需要采用廉价的粉末作原料时,经济问题便是先决条件。但是当需要粉末具有严格的性能要求时,则可选用昂贵的制粉方法。一些金属和合金粉末推荐的制取方法见表2。
表2 金属和合金粉末的推荐制取方法
金属或合金 |
推荐制取方法 |
铝 铜 铜合金 铁 钢 镍 精密合金 反应金属(钛、锆) 高熔点金属(钒、钼、铼、钽、铪) 特殊合金、超合金 |
气雾化,空气雾化,研磨 电解,水雾化,氧化物还原,硫酸盐沉淀 水雾化,机械研磨 氧化物还原,机械研磨,水雾化,离心雾化,电解,气雾化 气雾化,水雾化,蒸气雾化 羰基法,电解,氧化物还原,水雾化,气雾化 空气雾化,电解,混合还原 氯化物还原,离心雾化,化学沉积 氧化物还原,化学沉积,离心雾化 气雾化,水雾化 |
(二)粉末配制
粉末冶金成形前,要对粉末进行预处理及配制。预处理包括:退火、筛分、制粒等。
1. 退火 粉末的预先退火可使残留氧化物进一步还原、降低碳和其它杂质的含量,提高粉末的纯度,消除粉末的加工硬化等。用还原法、机械研磨法、电解法、雾化法以及羰基离解法所制得的粉末都要经退火处理。此外,为防止某些超细金属粉末的自燃,需要将其表面钝化,也要作退火处理。经过退火后的粉末,压制性得到改善,压坯的弹性后效相应减小。退火对粉末性能的影响见表3。
表3 不同条件下退火1h还原铁粉化学成分的变化
粉 末 |
退火条件 |
元素质量分数(%) | ||||
温度/℃ |
气 氛 |
wFe |
wC |
wMn |
wSi | |
原始粉末 退火粉末 退火粉末 退火粉末 退火粉末 |
— 800 800 1100 1100 |
— H2 H2+10%HCl H2 H2+10%HCl |
97.7 98.9 99.2 99.5 99.6 |
0.06 0.03 0.03 0.03 0.02 |
0.30 0.30 0.23 0.30 0.10 |
0.40 0.40 0.30 — 0.25 |
退火温度根据金属粉末的种类而异,一般退火温度可按下式计算:
T退=(0.5~0.6)T熔。
式中 T退——退火温度,单位为K;
T熔——合金的熔点,单位为K。
有时,为了进一步提高粉末的化学纯度,退火温度也可超过上述计算值。
退火一般用还原性气氛,有时也可用惰性气氛或者真空。要求清除杂质和氧化物,即进一步提高粉末化学纯度时,要采用还原性气氛(氢、离解氨、转化天然气或煤气)或者真空退火。为了消除粉末的加工硬化或者使细粉末粗化防止自燃时,可以用惰性气体作为退火气氛。退火气氛对粉末压制性能的影响见表4。
表4 退火气氛对粉末压制性能的影响
压坯压力/MPa |
压坯的孔隙率(%)(电解铁粉,750℃,2h) | ||
H2 |
HCl |
真空/Pa | |
200 400 600 800 1000 |
34.4 23.8 16.9 12.6 11.3 |
32.0 21.0 14.7 11.3 8.0 |
4 2.5 1.65 1.2 0.9 |
2.筛分 把颗粒大小不匀的原始粉末进行分级,使粉末能够按照粒度分成大小范围更窄的若干等级。通常用标准筛网制成的筛子或振动筛来进行粉末的筛分。
3.制粒 将小颗粒的粉末制成大颗粒或团粒的工序,常用来改善粉末的流动性。在硬质合金生产中,为了便于自动成形,使粉末能顺利充填模腔就必须先进行制粒。能承担制粒任务的设备有滚筒制粒机、圆盘制粒机和振动筛等。
4.混合 将两种或两种以上不同成分的粉末均匀混合的过程。有时需将成分相同而粒度不同的粉末进行混合,称为合批。混合质量不仅影响成形过程和压坯质量,而且会严重影响烧结过程的进行和最终制品的质量。
混合有机械法和化学法两种方法:
(1)机械法 常用的混料机有球磨机、V型混合器、锥形混合器、洒桶式混合器、螺旋混合器等。机械法混料又可分为干混和湿混。铁基等制品生产中广泛采用干混,制备硬质合金混合料则经常使用湿混。湿混时常用的液体介质为酒精、汽油、丙酮等。为了保证湿混过程能顺利进行,对湿混介质的要求是:不与物料发生化学反应,沸点低易挥发,无毒性,来源广泛,成本低等。湿混介质的加入量必须适当,否则不利于研磨和高效率的混合。
(2)化学法 将金属或化合物粉末与添加金属的盐溶液均匀混合,或者是各组元全部以某种盐的溶液形式混合,然后来制取如钨—铜—镍高密度合金、铁—镍磁性材料、银—钨触头合金等混合物原料。
粉末混合料中常常要添加一些能改善成形过程的物质,即润滑剂或成形剂,或者添加在烧结过程中能造成一定孔隙的造孔剂。这类物质在烧结时可挥发干净,例如可选用石蜡、合成橡胶、樟脑、塑料以及硬脂酸或硬脂酸盐等物质来做添加剂。
此外,生产粉末冶金过滤材料时,在提高制品强度的同时,为了保证制品有连通的孔隙,可加入充填剂。能起充填作用的物质有碳酸钠等,它们既可以防止形成闭孔隙,还会加剧扩散过程,从而提高制品的强度。充填剂常常以盐的水溶液方式加入。
(三)粉末成形
主要功能在于:
(1)将粉末成形为所要求的形状;
(2)赋予坯体以精确的几何形状与尺寸,这时应考虑烧结时的尺寸变化;
(3)赋予坯体要求的孔隙度和孔隙类型;
(4)赋予坯体以适当的强度,以便搬运。
根据成形时是否从外部施加压力,可分为压制成形和无压成形两大类。
压制成形主要有:封闭钢模冷压成形、流体等静压制成形、粉末塑性成形、三轴向压制成形、高能率成形、挤压成形、轧制成形、振动压制成形等;
无压成形主要有:粉浆浇注、松装烧结等。
下面着重介绍封闭钢模冷压成形方法。
封闭钢模冷压成形是指在常温下,粉料在封闭的钢模中,按规定的单位压力,将粉料制成压坯的方法。这种成形过程通常由下列工序组成:称粉、装粉、压制、保压及脱模。
1.称粉与装粉 称量形成一个压坯所需粉料的质量或容积。采用非自动压模和小批量生产时,多用质量法;大量生产和自动化压制成形时,一般采用容积法。
装粉方式有三种,如图4-6所示。落入法(图5a)是送粉器移送到阴模和芯棒形成的型腔上,粉末自由落入型腔中;吸入法(图5b)是下模冲位于顶出压坯的位置,送粉器被移送到型腔上,下模冲下降(或阴模和芯棒升起)复位时,粉料被吸入型腔中;多余充填法(图5c)是芯棒下降到下模冲的位置,粉末落入阴模型腔内,然后芯棒升起,将多余的粉末顶出,并被送粉器刮回,此法适用于薄壁深腔的压模。
图5 自动装粉方式
a)落入法 b)吸入法 c)多余充填法
2.压制 按一定的单位压力,将装在型腔中的粉料,集聚成达到一定强度、密度、形状和尺寸要求的压坯工序。
在封闭钢模中冷压成形时,最基本的压制方式有三种,如图6所示。其它压制方式,或是基本方式的组合,或是用不同结构来实现。
图6 三种基本压制方式
a)单项压制 b)双向压制 c)浮动压制
(1)压坯密度的均匀性 不同的压制方式,压坯密度的不均匀程度有差别。但无论哪一种方式,不仅密度沿高度分布不均匀,而且沿压坯断面的分布也是不均匀的。造成压坯密度不均匀的原因是在压制过程中,粉末颗粒之间、粉末颗粒与模冲、模腔壁之间存在磨擦,使压力损耗而造成的。采取各种措施,可减轻密度分布的不均匀性,但无法完全消除磨擦。
压坯密度的均匀性是其质量的重要标志,烧结制品的强度、硬度及各部分性能的同一性,皆取决于密度分布的均匀程度。此外,压坯密度分布不均匀,在烧结时将导致收缩不均匀,从而使制品中产生很大的应力,出现翘曲变形、甚至裂纹等。因此压制成形时,应力求使压坯密度分布均匀。
为了减小粉末颗粒与模壁之间的磨擦,延长压模的寿命,一方面可减小模壁的粗糙度;另一方面可在粉料中添加润滑剂。减小粉末与模壁之间的磨擦,可在相同的压力下,提高压坯密度和降低脱模力。常使用的润滑剂有石蜡、硬脂酸盐、油酸盐、樟脑、滑石、矿物油、植物油、肥皂、石墨及合成树脂等。
(2)压制过程 粉末装在模腔中,形成许多大小不一的拱洞。加压时,粉末颗粒产生移动,拱洞被破坏,孔隙减小,随之粉粒从弹性变形转为塑性变形,颗粒间从点接触转为面接触。由于颗粒间的机械啮合和接触面增加,原子间的引力使粉末体形成具有一定强度的压坯。
压制过程大体上可分为四个阶段:
①粉末颗粒移动,孔隙减小,颗粒间相互挤紧;
②粉末挤紧,小颗粒填入大颗粒间隙中,颗粒开始有变形;
③粉末颗粒表面的凹凸部分被压紧且啮合成牢固接触状态;
④粉末颗粒加工硬化到了极限状态,进一步增高压力,粉末颗粒被破坏和结晶细化。
实际上这四个阶段并无严格的分界,而且依据粉末的性能、压制方式及其它条件等有差异。
3.脱模 压坯从模具型腔中脱出是压制工序中重要的一步。压制时由于侧压力的存在,使阴模向外胀变形,而压坯是在已胀大了的阴模型腔中成形的。当卸压后,侧压力消失,阴模弹性恢复,向内收缩,压迫已成形的压坯,压坯产生抗压应力,迫使阴模收缩不到原位(指未压制时),而在某一位置达到阴模收缩力与压坯抗压应力之间的平衡,这个卸压后引起的力,叫做剩余侧压强。这个力的存在使压坯与模壁间产生很大的磨擦阻力,脱模力必须大于这个磨擦阻力,才能使压坯脱出型腔。
压坯从模腔中脱出后,剩余侧压强消失,阴模收缩到原位,压坯弹性恢复而胀大,这种胀大现象,叫做回弹或弹性后效。此值与模具尺寸计算有直接的关系。这种回弹可用回弹率来表示,即线性相对伸长的百分率。普通还原铁粉的压坯,其沿压制方向的回弹率约0.6%左右,垂直于压制方向约0.2%左右。
(四)烧结
烧结:压坯置于基体金属熔点以下温度(约0.7~0.8T,单位K)加热保温,粉末颗粒之间产生原子扩散、固溶、化合和熔接,致使压坯收缩并强化,这一过程称为烧结。
烧结对粉末冶金材料和制品的性能有着决定性的影响。烧结的结果是粉末颗粒之间发生粘接,烧结体的强度增加,密度提高。在烧结过程中,压坯要经过一系列的物理化学变化。开始是水分或有机物的蒸发或挥发,吸附气体的排除,应力的消除,粉末颗粒表面氧化物的还原;继之是原子间发生扩散,粘性流动和塑性流动,颗粒间的接触面增大,发生再结晶和晶粒长大等。出现液相时,还可能有固相的溶解和重结晶。这些过程彼此之间并无明显的界限,而是穿插进行,互相重叠,互相影响。加之一些其它烧结条件,使整个烧结过程变得很复杂。用粉末烧结的方法可以制得各种纯金属、合金、化合物以及复合材料。
在烧结过程中,固体颗粒表面能的减小是烧结的“推动力”,也即热力学条件。图7为颗粒聚结过程示意图。
假设原来有两个半径均为r的球形颗粒,当聚结为一个更大的半径为R的球时,根据体积不变原理,表面积由原来的8πr2变为6.35πr2,是一个表面能减小的过程。也就是说,烧结是一个自发的不可逆过程。
(五)后处理
金属粉末压坯烧结后的进一步处理,叫做后处理。后处理的种类很多,一般由产品的要求来决定。常用的几种后处理方法如下。
1.浸渍 利用烧结件多孔性的毛细现象浸入各种液体。如为了润滑目的,可浸润滑油、聚四氟乙烯溶液、铅溶液等;为了提高强度和防腐能力,可浸铜溶液;为了表面保护,可浸树脂或清漆等。浸渍有的可在常压下进行,有的则需在真空下进行。
2.表面冷挤压 为了提高零件的尺寸精度和减小表面粗糙度,可采用整形;为了提高零件的密度,可采用复压;为了改变零件的形状,可采用精压。复压后的零件往往需要复烧或退火。
3.切削加工 横槽、横孔,以及轴向尺寸精度高的面等。
4.热处理 可提高铁基制品的强度和硬度。由于孔隙的存在,对于孔隙度大于10%的制品,不得采用液体渗碳或盐浴炉加热,以防盐液浸入孔隙中,造成内腐蚀。另外,低密度零件气体渗碳时,容易渗透到中心。对于孔隙度小于10%的制品,可用与一般钢一样的热处理方法,如整体淬火、渗碳淬火、碳氮共渗淬火等。为了防止堵塞孔隙可能引起的不利影响,可采用硫化处理封闭孔隙。淬火最好采用油作为介质,高密度制品,若为了冷却速度的需要,亦可用水作为淬火介质。
5.表面保护处理 对用于仪表、军工及有防腐要求的粉末冶金制品很重要。粉末冶金制品由于存在孔隙,这给表面防护带来困难。目前,可采用的表面保护处理有蒸汽发蓝处理,浸油,浸硫并退火,浸清漆,渗锌,浸高软化点石蜡或硬脂酸锌后电镀(铜、镍、铬、锌等)、磷化、阳极化处理等。
(六)实例
1.粉末冶金工具材料及其成形
粉末冶金工具材料主要包括粉末高速钢、硬质合金和超硬材料等。
(1)粉末高速钢及其成形 高速工具钢由于具有优良的力学性能和耐磨性,广泛用来制作切削工具、成形工具和耐磨零件等。但是,用传统的铸锻方法生产的高速钢会产生偏析,从而形成化学成分不均匀、且晶粒粗大不匀的显微组织,降低了高速钢的韧度,影响了其使用性能。粉末高速钢由于其生产方法上的特点,可以使其具有细的晶粒结构,不存在碳化物聚集,将偏析降到了最低程度,因而提高了工具的寿命。
典型的粉末高速钢生产方法有三种:无偏析工艺(ASP工艺)、坩埚颗粒冶金法(CPM工艺)和全致密工艺。目前也有通过液相烧结来制取粉末高速钢的研究。
①无偏析工艺是将高速钢首先在惰性气体中雾化成粉末,然后将粉末振实、装入包套进行冷等静压制,再于高压、高温下将冷等静压后的坯料热等静压至完全致密。固结后,按常规的塑性成形方法将钢坯加工成所要求的尺寸。
主要优点:可以提高合金中合金元素的含量、碳化物分布均匀性和不产生合金缺陷,从而使粉末高速钢在提高耐磨性的同时不会降低其韧度,并具有较高的屈服强度。这种方法生产的粉末高速钢,按其合金成分不同,可分别用于:制造冷加工用的工具;对高温硬度有要求的切削工具;切削大多数不锈钢和高温合金的刀具;高速切削的场合以及切削极难加工的工具材料等。
②坩埚颗粒冶金法是将高压气雾化的预合金颗粒装入包套后进行热等静压,使之完全致密化。然后用常规的塑性成形方法将钢坯加工成所要求尺寸的坯料和棒料。这种工艺能将合金工具钢中的合金偏析减至极小。此外,还可以生产合金元素含量较高的工具钢。例如,CPMT15合金是标准工具钢材料中最耐磨最耐热的合金牌号之一,然而它的使用一直受到常规生产方法的限制,很难生产。只有使用坩埚颗粒方法之后才使得这种工具钢的生产成了可能。在CPMT15粉末高速钢中,大多数碳化物的尺寸都小于3μm,而常规方法生产的高速钢,有的碳化物尺寸可达到34μm,平均尺寸为6μm。表5为CPM工具钢的化学成分。其中CPM10V钢在高达480℃的温度下仍具有极好的耐磨性和韧度,可用作粉末冶金压制模具和许多其它的工具、模具,往往可以取代昂贵的硬质合金工具。T15粉末高速钢是航空工业中用来加工普通方法难以加工的高温合金和钛合金的主要切削工具钢。
表5 CPM工具钢的成分
合 金 |
组成(%) | |||||||
wC |
wCr |
wV |
wW |
wMn |
wMo |
wCo |
wFe | |
CPM10V CPM Rex76 CPM Rex42 CPM Rex25 CPM Rex20 CPM T15 |
2.40 1.50 1.10 1.80 1.30 1.55 |
5.30 3.75 3.75 4.0 3.75 4.0 |
9.8 3.0 1.10 5.0 2.0 5.0 |
0.3 10.0 1.5 12.5 6.25 12.25 |
0.5 —— —— —— —— —— |
1.3 5.25 9.5 6.5 10.5 —— |
—— 9.0 8.0 —— —— 5.0 |
其余 其余 其余 其余 其余 其余 |
③全致密工艺是用水雾化粉末进行冷等静压或模压成形,然后真空烧结到完全致密化。这种工艺可以大量生产尺寸精密、形状复杂的零部件。
优点:这种方法可以制造出相对密度接近100%的零部件,避免因含少量孔隙(即使是1%~2%)造成材料的淬硬性、伸长率、冲击韧度极大地降低。此外,这种工艺生产的零部件无需机械加工,从而可以减少材料的切屑,节约原材料。
粉末冶金高速钢的用途:制作铣刀铣削耐热高合金钢、奥氏体不锈钢,制作铰刀、丝锥和钻头等孔加工刃具,制作拉刀拉削渗碳钢、高温合金等难切削材料。还可用于制作齿轮滚刀,冲裁模具的冲头和凹模,冷镦、成形、压制和挤压模,以及滚丝模。此外,还可以用作冲孔工具材料等。
(2)硬质合金及其成形 硬质合金由硬质基体和粘接金属两部分组成。硬质基体保证合金具有高的硬度和耐磨性,采用难熔金属化合物,主要是碳化钨和碳化钛,其次是碳化钽、碳化铌和碳化钒。粘接金属赋予合金一定的强度和韧度,采用铁族金属及其合金,以钴为主。
硬质合金的品种很多,其制造工艺也有所不同,但基本工序大同小异,硬质合金的生产工艺流程如图8所示。
硬质合金是一种优良的工具材料,主要用于切削工具、金属成形工具、矿山工具、表面耐磨材料以及高刚性结构部件。硬质合金的种类、性能及用途见表6。
表6 硬质合金的种类性能及用途
种 类 |
性能及用途 | |
含钨硬质合金 |
WC-Co系 |
可用于加工铸铁等脆性材料或作为耐磨零部件和工具使用 |
WC-TiC-Co系 |
可用于加工产生连续切屑的韧性材料 | |
WC-TiC-TaC(NbC)-Co系 | ||
WC-TaC(NbC)-Co系 | ||
钢结硬质合金 |
以钢为粘接剂,碳化钛为硬质相。主要用作冷冲模、切削工具和耐热模具等 | |
涂层硬质合金 |
在硬质合金基体上沉积碳化钛,表面硬度高。适合于高速连续切削,工件表面质量好 | |
细晶粒硬质合金 |
高强度、高韧度和高耐磨性。用于加工高强度钢、耐热合金和不锈钢的切断刀、小直径的端铣刀、小绞刀、麻花钻头、微型钻头以及打印针和精密模具 | |
TiC基硬质合金 |
硬度HRA91~92、抗弯强度可达1930~1650MPa。可用于合金粗加工的高速切削 | |
碳化铬基硬质合金(CrC-Ni) |
常温及高温硬度高,耐磨性好,抗氧化性及耐腐蚀性能高。可作切削钛及钛合金的工具材料 |
2.粉末冶金多孔材料及其成形 采用粉末冶金方法制成的、孔隙度通常大于15%的金属材料。其内部孔隙弯曲配置,纵横交错,孔隙度和孔径大小可以控制和再生。具有优良、稳定的渗透性能,过滤精度高,具有足够的强度和塑性,有耐高温、抗热震等一系列优良性能。它可在高温或低温下工作,寿命长,制造简单。而普通滤纸、滤布的强度低,过滤速度慢,不能在高温下使用,并且难以再生,还易变形和难保证过滤精度。塑料多孔材料虽由球形颗粒制造,过滤性能好,但强度低,使用温度一般不超过100℃。陶瓷或玻璃多孔材料的塑性、可加工性和耐急冷急热性能差,因而应用有限。各种纺织用金属材料丝网孔易变形,影响过滤精度。粉末冶金多孔材料正好弥补了上述材料的不足,得到了较快的发展。
粉末冶金多孔材料因其高的孔隙度而有很大的孔隙内表面,决定了它具有许多特殊的物理化学性能和作用,例如物质的贮存作用,过滤和分离作用,热交换作用,吸附、催化作用,电极化作用以及不良的传导作用等,因而应用相当广泛。例如,利用其物质贮存作用可以制成含油自润滑轴承、含香金属制品;利用热交换作用可以制成宇航用发汗材料、氧-乙炔用防爆止火器;利用过滤和分离作用可以制成各种过滤器;利用其电极化作用可制成燃料电池的多孔电极等。粉末冶金多孔材料的应用举例见表7。
表7 粉末冶金多孔材料的应用
机能与特性 |
用 途 |
应用实例 |
过滤 |
气-固分离 |
过滤各种气体与气态化合物;高温烟气除尘 |
液-固分离 |
过滤各种油类、水溶液;合成树脂熔融物;熔融金属 | |
气-液分离 |
压缩空气除油、水;液压油除气泡 | |
液-液分离 |
油-水分离;水-药物分离 | |
分离浓缩 |
气体分离 |
混合气体分离;气体同位素分离 |
液体分离 |
渗透膜 | |
贯通孔透过特性 |
送入气体 |
物料输送板;硫化床;气体分布器;气体发散材料;气体喷射器 |
逸出气体 |
呼吸塞;透气性金属膜 | |
透过液体 |
雾化器;海水淡化支撑器;液体取样分析器 | |
吸收冲击 |
消音材料 |
压缩空气消音、吸音材料;声阻 |
缓冲材料 |
缓冲器(防止高能流体脉冲) | |
弹性压缩材料 |
封印材料;减震器 | |
大比表面积 |
化学反应 |
催化剂;催化剂载体;各种电极 |
热传导材料 |
热交换器;火焰阻止器 | |
毛细管现象 |
输送或供给液体 |
加湿器;燃烧嘴;灯芯;发汗冷却材料 |
控制流动 |
控制流动、流速 |
分流;分散板 |
控制气流层 |
控制喷射气体边界层,使紊流层流化 |
制造粉末冶金多孔材料的工艺流程如图9所示。
粉末冶金多孔材料使用的原料有各种纯金属、合金、难熔化合物等的球形和非球形粉末,以及金属纤维。常用的有铁、铜、青铜、黄铜、镍、钨、钛、不锈钢、镍-铜、碳化钨等粉末,以及不锈钢、镍-铬合金等纤维。制造粉末冶金过滤器大多用球形粉末或近球形粉末。
粉末冶金多孔材料可采用多种方法成形,如模压成形,等静压成形;松装烧结成形和注浆成形等。
3.粉末冶金贮氢材料及其成形 氢为理想的清洁能源,作为二次能源的开发利用倍受人们的关注。但如何简便、安全地贮存和运输是利用氢能的主要问题之一,利用金属氢化物来贮氢具有很强的吸引力。目前研究的贮氢材料有:
①以镧-镍为代表的稀土系;
②以钛-铁为代表的钛系;
③以镁-镍为代表的镁系材料。其中镧-镍为代表的贮氢材料是主要研究方向。某些金属氢化物的贮氢能力见表8。
表8 某些金属氢化物的贮氢能力和密度
储存介质 |
氢储存能力 |
能量密度 | |||
按质量 (%) |
按容量 /g·cm-3 |
按质量 /4.18J·g-1 |
按容积 |
释氢条件 | |
镁镍氢化物Mg2NiH4 钛铁氢化物TiFeH1.96 镧镍氢化物LaNi5H6 液态氢 气态氢 |
3.16 1.75 1.37 100 100 |
0.081 0.096 0.089 0.070 0.008 |
1071 593 464 33900 33900 |
2745 3254 3017 2373 271 |
250~300℃ 100℃以下 100℃以下 常温 常温 |
贮氢合金特性:
①大的贮氢比容;
②合适的应力特性;
③容易激活;
④氢气能快速被吸收和释放;
⑤良好的抗毒化性能,具有长的循环寿命;
⑥资源丰富而价廉。
由于贮氢材料在氢的吸收-释放过程中伴随着体积的变化,所以会出现如下一些现象:
①经过几次吸收-释放循环后,材料会发生碎化,形成非常细的粉末,增加了气体的流动阻力;
②氢化物的膨胀易引起容器壁的开裂;
③在热泵和化学压缩机的应用中,由于金属氢化物的吸附速率以及能量的输出。
这些现象限制了金属氢化物在工业上的应用。 一般用真空烧结方法来制取贮氢材料。