收藏词条 编辑词条 高炉炼铁
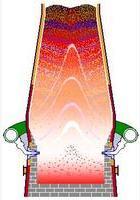
应用焦炭、含铁矿石(天然富块矿及烧结矿和球团矿)和熔剂(石灰石、白云石)在竖式反应器——高炉内连续生产液态生铁的方法。它是现代钢铁生产的重要环节。现代高炉炼铁是由古代竖炉炼铁法改造、发展起来的。尽管世界各国研究开发了很多炼铁方法,但由于此方法工艺相对简单,产量大,劳动生产率高,能耗低,故高炉炼铁仍是现代炼铁的主要方法,其产量占世界生铁总产量的95%以上。
简史
古代炼铁技术的发展
人类使用铁至少有五千多年历史,2500年前中国、印度、埃及等已能从矿石中提取铁。而高炉炼铁法的历史大约已有600年。原始的炼铁炉是由石堆炼铁法改造而成的。在土中挖一坑洞,周围用石块堆砌,称为地炉。以木炭为燃料,利用自然风力进行燃烧、加热和还原铁矿石,产品为类似块状的海绵铁。随着人力、畜力和水力鼓风方法的出现,产量提高,渣和铁也比较容易分离,产品质量有所改进。为适应冶炼难熔和难还原的矿石,需要增加炉子的高度,于是开始出现竖炉,但其产品仍是“熟铁球”,而含铁很高的炉渣则可以熔化成液体。14世纪中叶,最早的一批冶炼生铁的高炉出现了。由于水力鼓风的发展,高炉鼓风量增大,促使高炉炉缸温度提高,于是炉内海绵铁可以大量渗碳而熔化,就产生了生铁。然而由于生铁不能锻造,难以利用,当时称之为“猪铁”。经过把生铁和矿石一起装炉再一次熔炼,便得到熟铁,同时产量增加,自此形成了炼铁的二步操作法。二步炼铁法的出现是钢铁冶金史上的一个转折点,从此逐渐发展成近代钢铁冶金工业的工艺流程:第一步矿石在高炉中还原生成生铁;第二步在精炼炉中将生铁中的碳、硅等元素氧化而炼成熟铁和钢。进而发展为当前高炉炼铁——转炉炼钢的二步流程。
14世纪中叶的英国产业革命大大推动了经济技术的发展,高炉炼铁技术也有4项重大改进,为其后高炉逐步大型化和趋于完善奠定了基础。(1)焦炭的应用。由于炼铁用木炭要大量破坏森林,人们开始寻求用煤作燃料,但使用原煤在高炉内容易结焦和产生粉末,给冶炼带来很大困难,1735年英国人吉尔比(Gilbe)发明了一种得到焦炭的方法。以焦炭作燃料符合高炉冶炼要求,从而使生铁产量大幅度增长。(2)使用蒸汽鼓风机送风。18世纪中叶(1755~1765年间)英国人和俄国人分别以蒸汽机驱动鼓风机为高炉鼓风,从而促进了18世纪末高炉生铁产量的迅速增长,并为高炉大型化创造了条件。(3)预热鼓风。1828年苏格兰开始以热风炉给高炉预热鼓风,取得明显效果,推动了苏格兰高炉在10年间全部装备了热风炉。早期使用的是铸铁管换热式热风炉,加热空气的温度不超过400℃,1857年发明蓄热式热风炉后,风温急剧升高,促使燃料消耗大幅度下降,使高炉冶炼达到一个崭新的阶段。(4)高炉煤气的利用和封闭炉顶。1832年英国人第一次利用高炉煤气来加热鼓风,与此同时出现了封闭式炉顶。这两项新技术使当时的高炉生产和炉顶构造发生了巨大变化。
近代高炉炼铁技术的进步
自19世纪中叶起高炉炼铁发展速度加快,新技术不断涌现。择其要者可有11项:(1)采用精料。19世纪40年代开始生产人造富矿(烧结矿、方团矿和球团矿等)。起初烧结配料中不加熔剂,烧结矿是自然碱度的,到20世纪中叶发展为自熔性烧结矿,进而发展成熔剂性烧结矿,其冶金性能大为改善,高碱度烧结矿和球团矿成为高炉的主要原料,高炉基本上不再加石灰石。此外,矿石混匀、整粒、筛分等技术也有很大发展。与此同时焦炭质量也不断提高。这些,使高炉冶炼指标明显改善。(2)高炉大型化。1860年以前高炉最大容积为100~300m3 ,产量30~50t/d;到19世纪末容积增大到500~700m3,产量400~500t/d;进入20世纪炉容不断扩大到1000~3000m3,而到20世纪后期容积增大到4000~5000m3,最大的达5500m3,日产铁万吨以上。(3)上部和下部调剂技术。其内涵是对高炉上部调整装料制度(包括批重、装料顺序、料线、溜槽角位或活动炉喉挡位等)与下部调整送风制度(包括风口风速、鼓风动能及其他鼓风参数)相结合来获得高炉内合理的炉料分布和煤气分布,以达到炉子稳定顺行,煤气利用率高,焦比低的效果。为便于灵活布料,1970年卢森堡保尔渥斯公司(Paul Wurth)发明了无钟炉顶,于1972年首次在德国汉博恩厂应用后迅速推广,这是炉顶设备的又一次革命。(4)高压操作。以前高炉炉顶压力为0.01~0.02MPa,20世纪中期出现了高压(炉顶)操作,初期炉顶压力提高到0.07MPa左右,随着鼓风机能力加大,和设备制造水平提高,到20世纪后期炉顶压力已达到0.15~0.25MPa。由于炉内压力提高,煤气速度减慢,使高炉的冶炼强度和利用系数提高了一大步。(5)富氧鼓风。为减少煤气体积,利于炉况顺行,提高冶炼强度和产量,20世纪中叶出现了富氧鼓风技术,即在高炉鼓风中兑入一部分工业氧气。但由于风口前火焰温度的限制,这项技术在20世纪60年代高炉喷吹燃料技术发展起来以后,才得到广泛应用。(6)加湿鼓风与脱湿鼓风。为避免大气湿度波动对高炉冶炼产生不良影响和防止提高风温时风口前火焰温度过高导致炉况不稳定,50年代一度广泛应用加湿鼓风技术,即在鼓风中加入部分水蒸气,通过调整加入蒸汽的量来控制鼓风湿度。60年代起高炉大量喷吹燃料以后,风口前的火焰温度已不是过高而是常常不足,于是加湿鼓风逐渐用得少了,反而又出现了脱湿鼓风技术,即将鼓风中的自然水分脱除到适当水平以保持风口前适当的火焰温度,同时又使鼓风湿度保持稳定。(7)高风温技术。随着原料的改善,喷吹燃料技术的发展,操作水平的提高,以及热风炉构造和耐火材料的改进,高炉风温水平从20世纪中期的500~600℃提高到20世纪后期的1100~1350℃。由于风温水平大幅度提高,焦比显著降低了。(8)喷吹燃料技术。为大量降低高炉焦比,60年代起普遍采用了从高炉风口喷吹燃料的技术。喷吹燃料的种类主要有重油、天然气和煤粉。由于喷重油和天然气比喷煤粉设备相对简单,60~70年代多数高炉都喷重油和天然气,只有美国和苏联的少数几座高炉喷煤粉。中国根据自己的资源特点重点发展了喷煤粉,到70年代末全国重点钢铁企业已有40座高炉喷煤粉,占当时重点钢铁企业高炉总数的54.8%。1966年首都钢铁公司的高炉平均喷煤量达到159kg/t,焦比降到476kg/t,其中1号高炉年平均喷煤225kg/t,最好的月份喷煤量达2。79kg/t,焦比为336kg/t,创世界喷煤最高纪录。当时中国喷煤高炉之广,喷煤量之多,引起世界瞩目。80年代起,由于油价高涨,焦炉老化,炼焦煤和焦炭短缺,以及环保对焦炉的限制等因素,世界高炉迅速转向喷煤,到90年代喷煤量多的已达到200kg/t以上,焦比降到300kg/t以下。(9)低硅生铁冶炼技术。由于降低生铁含硅量高炉可以降低焦比和提高产量,同时对转炉炼钢也有好处;也由于原料改善,风温提高和操作水平提高,为降硅创造了条件,20世纪后期炼钢生铁含硅量逐步降低,到20世纪末,许多高炉的生铁含硅量已降到0.2%~0.3%的水平。(10)高炉长寿技术。随着原料质量和操作水平的提高,以及高炉耐火材料质量的改进(包括碳砖和碳化硅砖等优质耐火材料的应用)和冷却方法的进步,70年代以后,高炉寿命显著延长,到90年代已达到10~15年,最高达到20年。一代炉役单位炉容产铁量达到7000~9000t/m3,高的达到12000t/m3。(11)自动控制技术。随着机械化、自动化技术的发展和电子计算机的应用,高炉的自动控制水平在20世纪后30年间有很大发展。不仅上料系统、热风炉燃烧和换炉、炉前操作等各环节实现了自动化操作,炉内冶炼过程控制也由于人工智能、专家系统的应用有很大提高。
中国高炉炼铁的发展
中国炼铁始于2500年前的春秋、战国之交,当时铁广泛应用于武器、农具和家庭用具。汉武帝时(公元前110年),将炼铁收归官营,先后设立了49个铁官。东汉时发明了以水力代替人力鼓风,有力地推动了炼铁生产的发展。1400年前的南北朝时代,在一些冶铁炉上已开始用煤。使用木制风箱鼓风也比较早。这些事实说明中国古代炼铁技术的发展在世界上是较早、较快的。后来由于长期的闭关自守,炼铁技术逐渐落后。19世纪下半叶清政府为发展近代军事和民用工业,开始兴办近代矿冶工业。1890年湖广总督张之洞主持兴建的汉阳铁厂是中国第一个近代炼铁企业。该厂在1894年建成两座248m3高炉(每座日产生铁100t左右),因为焦炭要从德国进口,所以到1896年才正式出铁。1908年盛宣怀将汉阳铁厂由官办改为官督商办,成立汉冶萍煤铁厂矿公司,自己生产焦炭,并在1910年新建477m3高炉(日产生铁250t左右),使该公司成为当时东亚最大的钢铁企业。辛亥革命后在大冶新建两座650~700m3高炉(日产生铁各450t左右),汉阳铁厂又添建一座477m3高炉。在第一次世界大战期间钢铁价格高涨,汉冶萍公司的生产有发展,但战后钢铁价格暴跌,该公司走向衰落,1925年被迫停产。除汉冶萍公司外,第一次世界大战前后(1915~1920年间),本溪、鞍山、上海、阳泉、石景山等地也先后建起高炉10余座(其中200~695m3高炉7座,其余为100m3以下的小高炉),使1920年生铁年产量达到43万t,但因钢铁价格下跌,导致部分厂关闭,使往后的几年里,生铁年产量降到40万t以下。1931年“九•一八”事变和1937年“七•七”事变后,日本侵略者对我国资源大肆掠夺,在其占领区新建了一批高炉和铁厂。与此同时当时的中国政府将汉阳铁厂、六河沟铁厂、上海钢厂等内迁,在四川、云南建设一批小钢铁厂投入生产。这样,国民党统治区和日本占领区的生铁产量在1942年达到最高的年产量178.7万t(其中,国统区7.8万t,敌占区170万余t)。1945年日本投降,大部分钢铁厂被破坏,生铁年产量降到不足20万t,到1949年中华人民共和国成立前,全国能开工的高炉只有9座。在抗日战争和解放战争时期,解放区的军民和科技人员在极端困难的条件下于1938年建起柳沟铁厂,1942年在延安建成一座近代小高炉,1946年在长治建钢铁厂,先建成一座小高炉,后又将阳泉的20t高炉迁建到该厂,1947~1948年又恢复阳泉的1号和3号高炉。解放区的炼铁工业虽然规模不大,设备也较简陋,但有力地支援了革命战争,造就了一批技术和管理干部。1949年中华人民共和国成立后,迅速对原有高炉进行了恢复和改造,使生铁产量迅速增加,1949年全国生铁产量只有19万t,到1957年就上升到593万t。1958~1978年间有武汉钢铁公司、包头钢铁公司、攀枝花钢铁公司等数十家新建钢铁企业投入生产,加上老厂扩建,新增高炉有百余座之多,使1978年生铁产量增加到3470万t。1978年实行改革开放政策以后,中国炼铁事业的发展速度进一步加快,1978~1998年间又新建和改造成包括宝山钢铁集团公司的4063~4350m3高炉在内的一大批现代化大高炉,加上新增的一大批300m3小高炉在内,新增容积约8万m3。1997年统计,全国有高炉3228座(其中大于1000m3的44座),年产生铁能力12648万t。1993年全国生铁年产量达到8730万t,从这一年起中国成为世界上产铁最多的国家,1995年以后生铁年产量一直在1亿t以上,1998年达11860万t,占全世界生铁产量的1/5以上。在产量增加的同时,高炉的技术经济指标也不断改进。1998年宝山钢铁集团公司高炉平均利用系数达2.051t/(m3•d),焦比320kg/t,煤比172kg/t;而自1998年以来至今1年多的时间里,利用系数一直在2.2~2.3t/(m3•d),平均焦比300kg/t,煤比200kg/t左右,居世界先进行列。一大批300m3级的小高炉利用系数高达2.5~3.0t/(m3•d),并且它们还具有投资省、建设快、原料适应性强等特点;这批小高炉中许多成功地采用了干式(布袋)煤气除尘和球式热生泡沫渣、粘渣,渣铁热结放不出来,以及铁损过高等一系列技术难题,技术经济指标逐年改善,1998年攀枝花钢铁公司高炉在入炉矿含铁仅有46.62%,炉渣中TiO2 达22%~24%的条件下,利用系数达到2.167t/(m3•d),焦比524kg/t,煤比74.9kg/t。(见钒铁磁铁矿的高炉冶炼)。1959年包头钢铁公司高炉开始用含氟、碱金属和稀土元素的白云鄂博铁矿进行冶炼。经过多年探索,解决了风口、渣口、铁口经常损坏,频繁结瘤和产生炉缸堆积等许多技术难题,生产指标逐步改善,1998年高炉利用系数达到1.568t/(m3•d),焦比485kg/t,煤比81.5kg/t。(见白云鄂博矿的高炉冶炼)
在钢铁冶金中的地位
高炉不仅生产铁,而且还副产高炉煤气和高炉渣。高炉铁水是炼钢转炉的基本原料;高炉煤气是钢铁联合企业的重要气体燃料;高炉渣经水淬成水渣后是生产矿渣水泥的原料。高炉生产是否稳定直接影响到钢铁联合企业的生产能否正常、稳定、均衡地运行,高炉铁水的质量更直接影响炼钢生产和钢水及钢材的质量。炼铁是能耗大户。高炉、烧结、炼焦三个工序的能耗在钢铁联合企业总能耗中约占70%,单是高炉的能耗即占50%左右。炼铁又是钢铁联合企业产生环境污染的重点户。高炉和烧结的烟尘,焦化的废水和烟尘对环境污染都是严重的,故它又是钢铁企业环境治理的重点部门。
工艺流程
自然界的铁大多是以铁的氧化物状态存在于矿石中。高炉炼铁即是利用还原剂从铁矿石的氧化铁中夺取氧而提取金属铁的一个连续生产过程。冶炼工艺流程见图1。铁矿石、焦炭和熔剂等原、燃料按规定配料比由炉顶装料设备分批装入高炉,并使炉喉料面保持一定高度。焦炭和矿石在炉内形成交替分层结构。鼓风机送出的冷风经热风炉加热到800~1350℃以后从风口吹入炉缸,热风使风口前的焦炭和经风口喷入炉内的煤粉、重油、天然气等燃烧,产生2000~2350℃炽热含CO和H2 的还原性煤气。这种高温煤气流在上升过程中与铁矿石、熔剂之间进行激烈的传热、传质、传递动量过程。铁矿石中的氧化铁在下降过程中逐步被CO、H2 和固体碳还原成金属铁,经渗碳、熔化成为生铁。铁矿石中的杂质与熔剂结合成为炉渣。液态生铁和炉渣聚集在炉缸,定期或连续从铁口和渣口排出。上升的煤气逐渐冷却,从炉顶逸出,经除尘后供做燃料使用。炉料在下降过程中温度逐渐上升,当被加热到100~200℃时,其中的水分即蒸发,褐铁矿和某些脉石中的结晶水要到500~800℃才分解蒸发;熔剂石灰石和白云石以及其他碳酸盐和硫酸盐在炉中受热分解,石灰石中CaCO3和白云石中MgCO3 的分解温度分别为900~1000℃和740~900℃;铁矿石在高炉中于400℃或稍低温度下开始还原,部分氧化铁是在下部高温区先熔于炉渣,然后再从渣中还原出铁,主要反应如下:
焦炭在高炉中不熔化,少部分焦炭在下降过程中参与还原时气化成CO,大部分是到风口前燃烧气化。矿石在部分还原并升温到1000~1100℃时开始软化,到1350~1400℃时完全熔化,超过1400℃就滴落。矿石在软化和熔化过程中已还原出来的铁经过渗碳变成液态生铁,其脉石则与熔剂结合形成液态炉渣。在矿石软熔以前,焦炭和矿石一直保持分层结构(混装例外)。由于高炉中的逆流热交换,形成了温度分布不同的几个区(带)(见图2)。图中①是矿石与焦炭分层的干区称块状带;②是从矿石开始软化到完全熔化,由软熔层和焦炭夹层组成的区域称为软熔带;③是液态渣铁穿过高lllgao固体焦炭层滴落的区域称滴落带;④是风口前一个袋形的风口回旋区。焦炭在这个区内强烈回旋与燃烧,是炉内热量和还原剂的主要发源区。这部分和炉缸集聚渣铁区域一起称为风口炉缸带,此处铁水温度一般为1400~1550℃,渣水温度比铁水还要高30~70℃。
主要设备
包括高炉本体、送风设备、上料设备、渣铁处理设备、煤气除尘设备和检测控制设备等。
高炉本体
呈竖式圆筒状,外壳用钢板制成,内砌耐火砖,砖与炉壳之间有冷却器。顶部有装料设备,分钟式和无钟式两种;下部炉缸有出铁口和出渣口(多铁口高炉没有出渣口,炉渣在出铁过程中从铁口排出),炉缸上沿有风口。所用耐火砖按不同部位有碳砖、高铝砖、碳化硅砖、铝碳砖和黏土砖等;冷却器有冷却壁、冷却板和冷却箱等几种形式。(见高炉)
送风设备
包括鼓风机、热风炉及相关的各种阀门。送风系统和高炉之间用管道连接。鼓风机有蒸汽驱动和电力驱动两类。通常一座高炉需3或4座热风炉轮流加热和送风,其形状为立式圆筒状,外壳用钢板制成,内砌耐火砖。根据燃烧室的设置不同,热风炉分为内燃式、外燃式和顶燃式三种。(见热风炉)
上料设备
主要有料仓(用以接纳从烧结或球团厂、炼焦厂和贮料场运来的原料和焦炭)、筛分设备、称量装置、炉顶装料设备、皮带运输机和有关闸门等。各设备之间主要靠皮带运输机连接。往炉顶上料的方式小炉子一般用料车卷扬机经过斜桥运输,大炉子多用皮带运输机运输。
渣、铁处理设备
在炉前有开铁口用的开口机、堵铁口用的泥炮和堵渣口用的堵渣机;出铁场上有铁水流槽、冲水渣设备和出铁场用的吊车;还有运输铁水用的铁水罐、鱼雷车以及铸铁机等。
煤气除尘设备
包括重力除尘器、洗涤塔、文氏管、脱水器(如采用干法除尘,则在重力除尘器后接布袋除尘器或电除尘器);此外,还有炉顶压力调节装置、余压发电设备以及有关阀类。炉顶与各除尘设备之间用管道连接。
检测控制设备
主要有炉体和炉内各部位的温度、压力、料线、以及煤气和炉料分布状况方面的检测装置;鼓风的流量、压力、温度、湿度、富氧量和煤顶煤气的温度、压力等参数的检测和相关的控制设备;原、燃料、生铁、炉渣和炉顶煤气成分的化学分析设备;上料系统和热风炉燃烧、换炉的程序控制等。所有检测到的数据都输入计算机进行贮存、分析、推理,并由计算机发出指令直接进行调控或向操作人员提出建议。
产品、产率、消耗
高炉的主要产品是生铁,按成分和用途不同分为炼钢生铁和铸造生铁,小高炉也可生产锰铁和硅铁。副产品是高炉煤气和炉渣。1m3 高炉有效容积日产生铁1.6~3.0t;每产lt生铁可产高炉煤气1500~2500m3 ,产炉渣0.2~0.8t。每产lt生铁消耗铁矿石1.5~2.0t,熔剂(含烧结生产过程中消耗的石灰石和白云石)0.2~0.3t,燃料0.46~0.65t(其中焦炭0.25~0.55t,其余为喷入的煤粉、重油或天然气),鼓风1000~2000m3 。